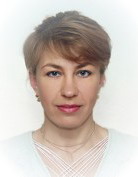
Маргарита Черненко,
СМС, управляющий партнер Бюро Бизнес Инжиниринга
Бережливое производство (Lean) - это интерпретация идей Производственной системы компании Toyota американскими исследователями ее феномена. Отцом этих идей считается Тайити Оно, начавший работу в Toyota Motor Corporation в 1943 году. В середине 1950-х годов он начал выстраивать особую систему организации производства, названную Toyota Production System. Позже эта система стала известна в западной интерпретации как Lean production, Lean manufacturing, Lean. Термин Lean был предложен Джоном Крафчиком, одним из американских консультантов.
Как мы осваивали Lean
Репортаж о проведении деловой игры Lean. Участие в деловой игре Lean позволило участникам на практике понять основные аспекты системы Lean (Бережливое производство). Начав с традиционного подхода к производству, участники последовательно применили основные принципы Lean и завершили работу в условиях применения системы канбан.
4 октября. Солнце ярким светом буквально заливает помещение, котором мы будем работать сегодня, создавая приподнятое настроение и желание рваться в бой. И это очень важно, ведь сегодня мы будем знакомиться с Lean методами управления производством. Помещение разделено на две части. В одной части будет проходить теоретическая часть – знакомства с методиками Lean, во второй, - рабочей области будет происходить практическая отработка этих методик. Здесь на модели будет воспроизведен процесс производства электрических вилок. Это деловая игра.
Накануне приехал Андрей - консультант компании «Райтстеп», нашего российского партнера, который и будет обучать нас методам Lean. С собой он привез реквизиты деловой игры. Когда мы планировали это мероприятия, наши российские коллеги реквизит ласково называли «наш волшебный чемоданчик». На поверку «чемоданчик» оказался чемоданищем, в котором аккуратно в ящичках и коробочках разложены детали, винтики, гаечки, инструменты, инструкции и т.д., - все, что нужно для процесса производства.
Подготовка
Участников еще нет, и мы организуем пространство для сегодняшней работы. Андрей просто вываливает все содержимое чемодана на стол в рабочей области, где будет создаваться модель производства, перемешивает его и бросает чемодан сверху [Фото 1].
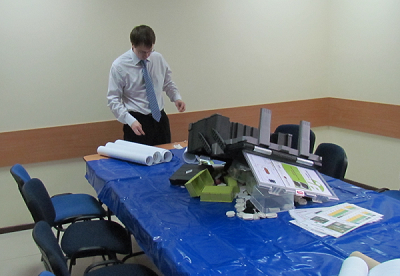
- «Что ты делаешь? Зачем ты идеальный порядок превратил в бардак?» - задаю я вопрос.
- «А вы видели, как размещаются на рабочих местах или хранятся детали и инструменты на среднестатистическом производственном предприятии?» - в свою очередь задает вопрос Андрей.
- «Ну, в общем-то, да».
- «Ну и как, есть там порядок?»
- «Как, правило, нет».
- «Ну, тогда и начнем работать в тех условиях, в которых обычно работают рабочие на предприятиях».
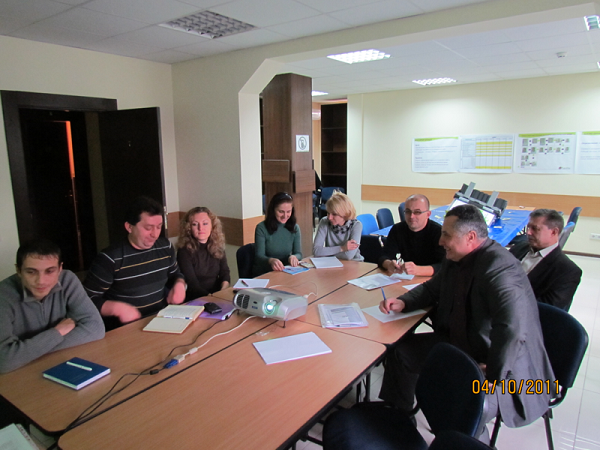
Фото 2
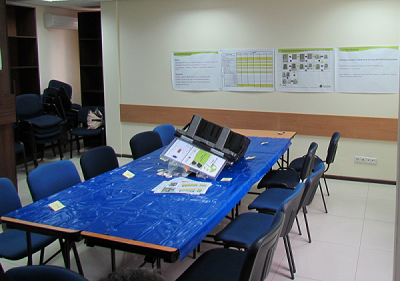
Фото 3
Понемногу собираются участники. Они занимают места за столом, в той части помещения, где будет проходить теоретическая часть работы. Их немного, 9 человек, так как условия деловой игры ограничивают количество непосредственных участников. Периодически они недоуменно поглядывают на ту часть помещения, где будет проходить практическая работа, на огромный стол в этой части, заваленный деталями и инструментами [Фото 2, Фото 3].
Мы начинаем. Андрей рассказывает наши цели на сегодня:
Понять, что есть Lean «на самом деле»
«Примерить» Lean на себя, понять цели, которые предстоит достичь компании и необходимость изменений
Изучить основные методы построения Lean
Понять последовательность реорганизации производства по Lean
Начать думать и действовать в соответствии с концепцией Lean
Теория: В чем отличия Lean от традиционных методов управления?
Потребительская ценность - отправная точка Lean
Ответим на вопрос: «Что клиент покупает у компании?» Клиент всегда покупает то, что имеет для него ценность, ценность с точки зрения удовлетворения его потребностей, какими бы они ни были (материальные, нематериальные, имиджевые и т.д.). Эту ценность чаще всего называют потребительской ценностью. И клиент готов заплатить за эту ценность ровно столько, насколько она для него ценна. Действия компании, по сути, направлены на то, чтобы создать для клиента эту ценность. Однако во всем этом существует один аспект - все действия компании можно разделить на две группы: операции, непосредственно связанные с созданием потребительской ценность (т.е. создающие дополнительную ценность – ДЦ), и операции не создающие ценности. Самыми простыми примерами операций не создающих потребительской ценности, является выпуск некачественной продукции, переделка работы, перемещения изделий между участками, хранение, контроль качества (как не странно, но операции контроля качества дополнительной ценности не создают), и т.д. По сути, операции, не создающие потребительской ценности, являются или «неизбежным злом», или потерями. Потери — это любое действие, которое потребляет ресурсы, но не создает ценности для потребителя.
Западные исследования показывают, что доля операций, создающих потребительскую ценность (ДЦ) в общем объеме операций компаний намного ниже, чем доля операций, не создающих ценность (ПОТЕРИ) [Рис. 1].

Фокусом традиционного подхода в управлении является сокращение времени операций, создающих потребительскую ценность, в частности решения приобретения более производительного оборудования. Однако, эффект оказывается незначительным или вообще отсутствует. «Это точно, как у нас», - говорит один из участников. - «Уже и новое оборудование закупили на миллионы долларов, а все равно выполнять заказы клиентов не успеваем. Хотя как не зайду в цех, в 50 процентов случаев новое оборудование простаивает».
Однако, так как операции, не создающие ценности (потери) имеет высокую долю в общем объеме, то логика того же правила Парето (20:80) говорит о том, что сокращение этих операций может дать более значительный эффект. Поэтому Lean фокусируется на оптимизации производства через сокращение потерь [Рис. 2].
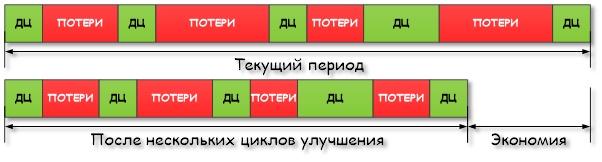
Мы рассматриваем подход Lean к классификации производственных операций. Основной принцип классификации - фокус на том, что важно для клиента [Рис 3].
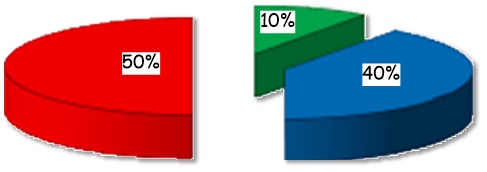
10% - Все операции, которые изменяют характеристики продукта, его форму и технические показатели, согласно требованиям заказчика. Их не обходимо оптимизировать.
40% - операции, не добавляющие ценность, но необходимы, из-за текущей организации производства. Их необходимо уменьшить.
50% - Потери - все бесполезные операции (7 видов потерь, которые будут рассмотрены далее). Их необходимо устранить.
Эта диаграмма отображает современное состояние производственной системы Toyota, так как это оценивает сама компания. Когда компания только начинала создавать свою производственную систему, добавленная ценность операций, по собственной оценке компании, составляла всего 1%.
Участники долго спорят, что все-таки принесет больший эффект: оптимизация полезной работы или избавление от потерь. К общему мнение пока прийти не могут.
- «Давайте на практике убедимся, в том, что приносит больший эффект», - говорит Андрей. - «Ведь именно для этого мы сегодня здесь и собрались».
Этап 1: Первый производственный цикл – работаем как всегда
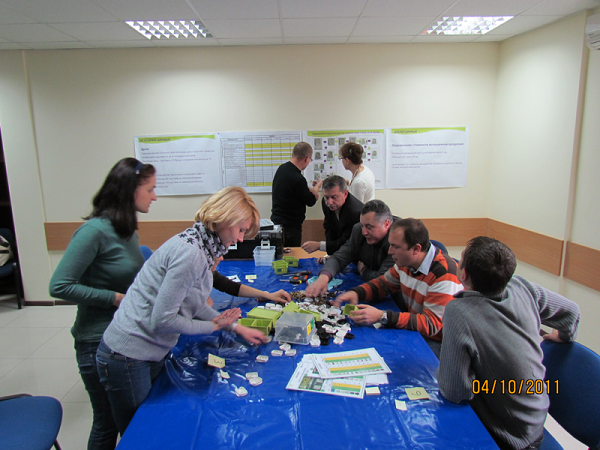
Фото 4
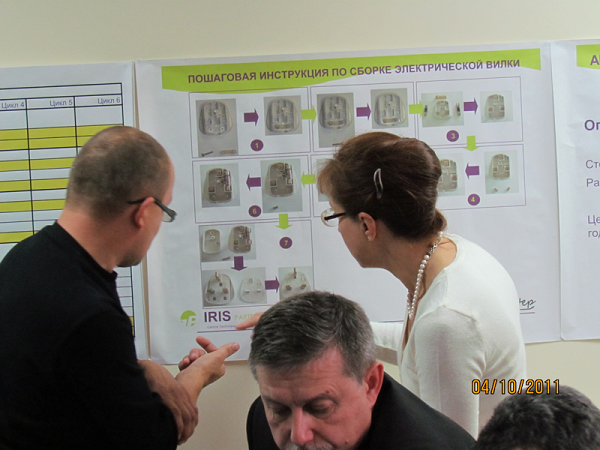
Фото 5
Мы переходим к практической работе, и вся группа перемещается в часть помещения для практической работы, все занимают места за столом [Фото 4]. Андрей объясняет условия и распределяет роли участников в производственном процессе.
На стене показана схема пошаговой сборки электрической вилки [Фото 5]. В производстве 7 участков. Каждый участник – это один участок. Так как участников 9, на некоторых участках будут работать по два участника. Производственные участки пронумерованы, но на площади стола располагаются в произвольном порядке (что, в общем-то, соответствует обычной производственной практике, когда детали хотят в производстве по очень сложным маршрутам)
Цели производства следующие
Заказчик желает получить 25 белых электрических вилок, заданного качества, в заданный промежуток времени
Необходимо произвести 25 вилок за 15 мин и произвести их по конкурентной цене. Стоимость выпущенной продукции определяется по формуле:
Себестоимость вилки = (Стоимость материалов + Стоимость работы) / кол-во годных выпущенных вилок
Стоимость материалов для одной вилки равна 1 ед.;
Рабочий час стоит 20 ед.
Вилки производятся партиями по 5 штук
Дополнительные правила игры, которые позволяют максимально воспроизвести производственные условия
Помогать другим нельзя, выполнять только свою работу
Собирать вилки до тех пор, пока не закончится время
Собирать вилки до тех пор, пока не закончатся детали
Партия производства в 5 штук передается с участка на участок операцией перемещения, которую участник выполняет, двигаясь по часовой стрелке вокруг стола (передавать детали с участка на участок через стол запрещено).
Начинаем первый производственный цикл – обычная работа среднестатистического предприятия. Мы засекаем время.
Участники лихорадочно набирают себе детали и инструменты [Фото 4]. Начинается работа. Пока первый участок выполняет свою работу – первую операцию и формирует партию из 5 вилок, все остальные участки сидят в ожидании [Фото 6] (совсем как на заводах, - кто-то работает в «три пота», а кто-то ждет, потому что «детали не подвезли»).
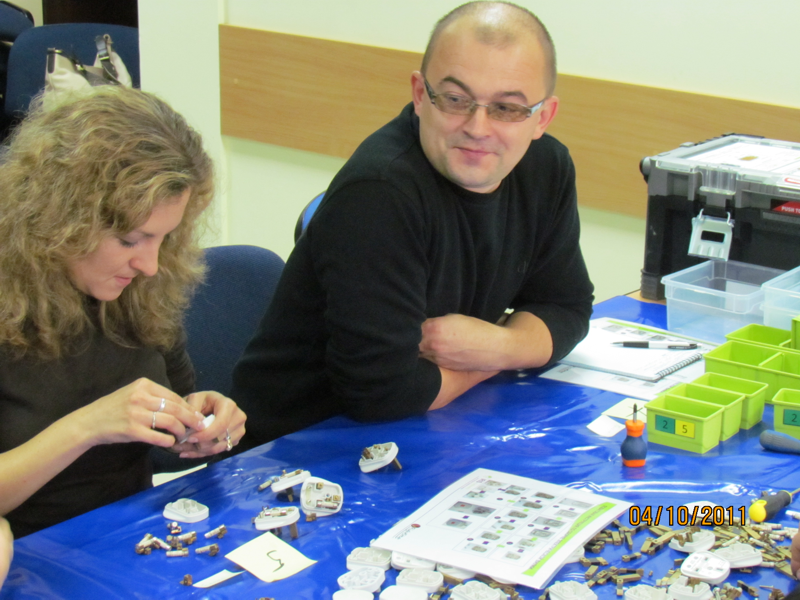
Фото 6
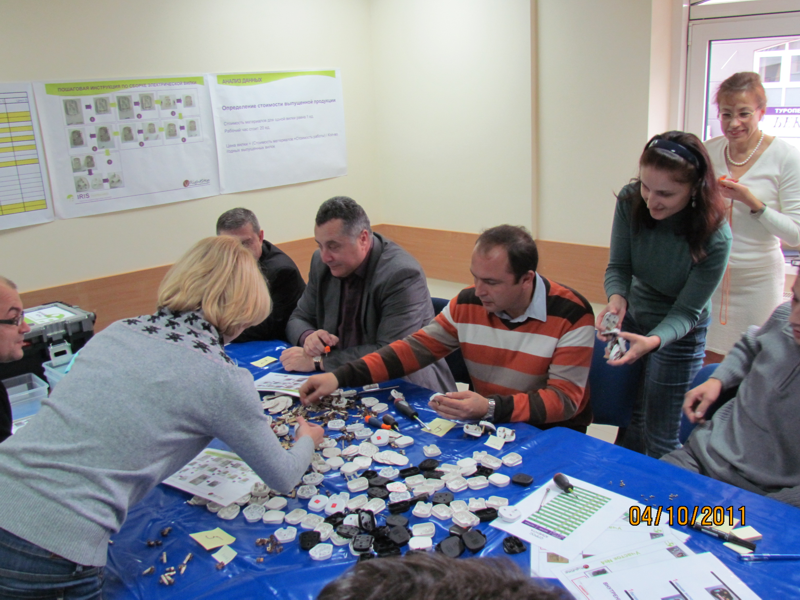
Фото 7
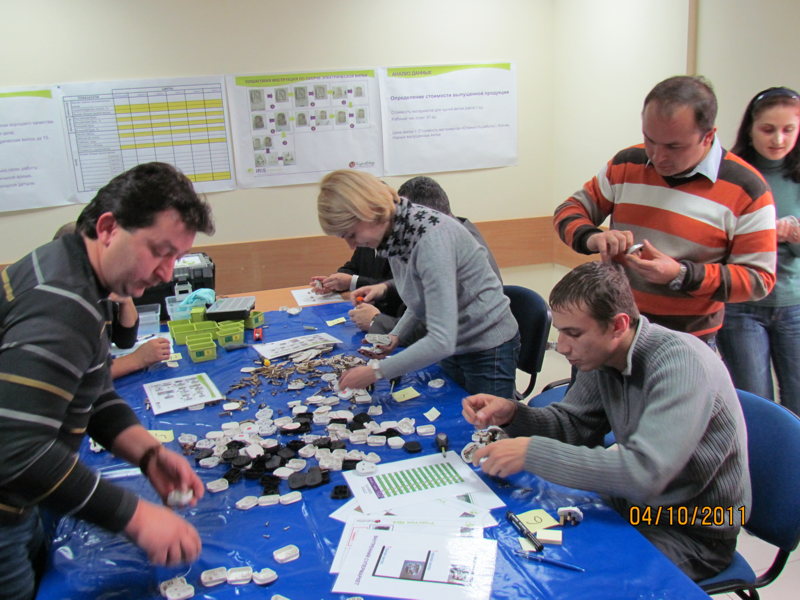
Фото 8
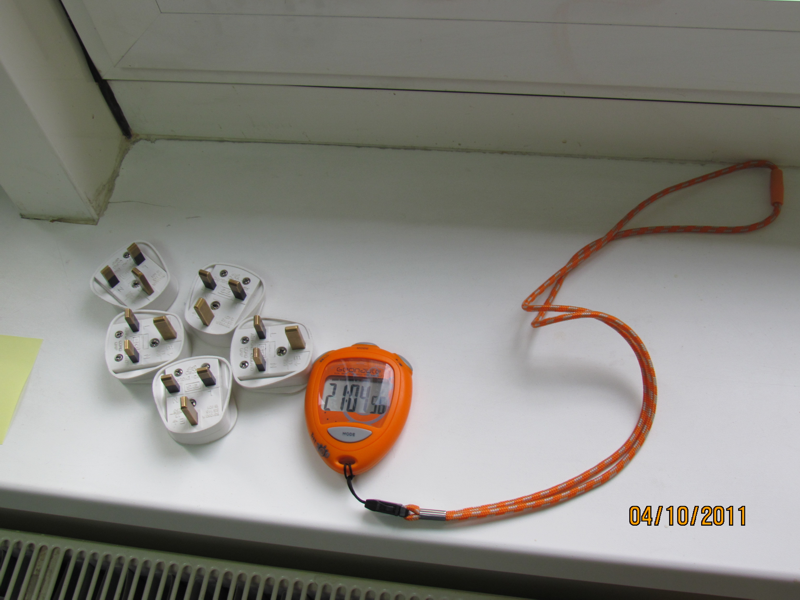
Фото 9
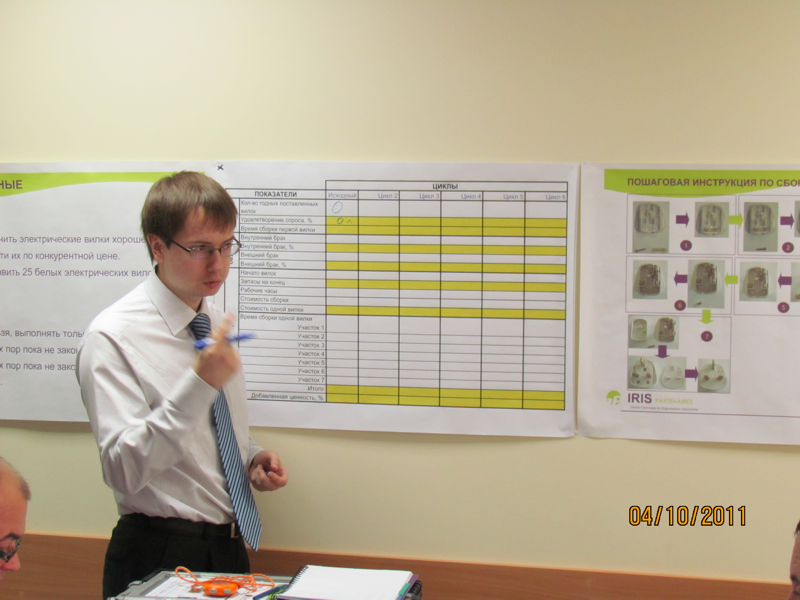
Фото 10
Постепенно в работу включаются все участки. Работа кипит, все лихорадочно стараются как можно быстрее выполнить операции на своих участках и буквально бегом несут детали на следующий участок [Фото 7].
На участках нет никакого порядка: детали, поступившие на участок, детали для сборки, детали произведенные, инструменты, инструкции перемешаны все перемешано – ну как обычно в производстве [Фото 8].
Вот и финал [Фото 9] – пять вилок из производства вышло через 21 минуту 4,56 сек.
Ура! Однако радость была преждевременной.
Андрей проверяет качество вилок. Оказывается, все они имеют внешний
брак: сопровождаются неправильными этикетками, - на этикетках указан ток, превышающий физические параметры вилки и вилки выбраковываются. И так подводим итоги эффективности нашего первого цикла [Фото 10] производства и рассчитываем показатели производства [Таблица 1].
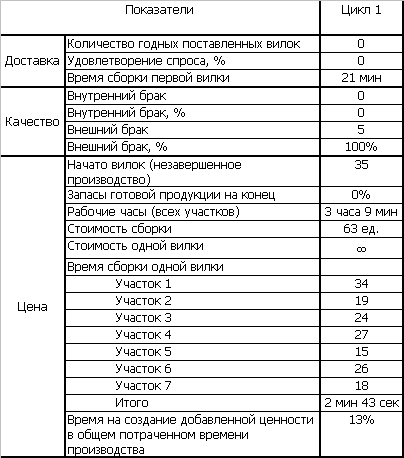
Вывод 1: Только 13 % из общего рабочего времени было затрачено на создание добавочной ценности.
Но, радоваться не чему. По условию, заказчик хотел получить 25 вилок за 15 минут, а мы произвели 5 бракованных вилок за 21 минуту. В реальной жизни клиент уже бы ушел к конкуренту, который способен удовлетворить его потребности в заданном количестве, заданного качества, в заданный промежуток времени по приемлемой цене.
Наш результат просто катастрофический.
Обратим также внимание, что длительность цикла производства составила 21 минуту, в то время как чистое время цикла сборки одной вилки всего 2 мин. 43 сек. Это то же свидетельствует о непроизводительных потерях.
«Ну и как вам наше производство?» - задает вопрос Андрей, - «Всех ли оно устраивает?».
Все соглашаются, что так работать нельзя и начинается активное обсуждение, что можно улучшить.
«Конечно, улучшить можно много чего», - говорит Андрей, «Но начинать стоит с самого простого – наведения порядка на рабочих местах в цехах».
Разбираем все собранные и полусобранные вилки и переходим ко второй части – изучение, что такое Lean.
Теория: Что такое Lean
Lean - это концепция менеджмента (идеология и набор методологических инструментов), применение которой нацелено на увеличение доли времени операций, создающих добавленную ценность, в общем операционном времени путем постоянного стремления к устранению всех видов потерь.
Применение концепции Lean на практике означает именно постоянную борьбу с потерями, а не традиционную борьбу с затратами путем их «урезания». В результате применения Lean сокращение затрат происходит само собой, как следствие борьбы с потерями.
Первый практический инструмент Lean – 5S
Первым практическим инструментом Lean является система 5S — система организации и рационализации рабочего места. Система включает в себя соблюдение 5-ти принципов:
Сэири (Sort) «Сортировка» — чёткое разделение вещей на нужные и ненужные и избавление от последних [Рис. 4].
Сэитон (Set in order) «Соблюдение порядка» — организация хранения необходимых вещей, которая позволяет быстро и просто их найти и использовать [Рис. 5].
Сэисо (Shine) «Содержание в чистоте» — соблюдение рабочего места в чистоте и опрятности [Рис. 6]
Сэикэцу (Standardize) «стандартизация» — необходимое условие для выполнения первых трёх правил. Это формальное, письменное закрепление правил содержания рабочего места, технологии работы и других процедур [Рис. 7].
Сицукэ (Sustain) «совершенствование» (формирование привычки) — воспитание привычки точного выполнения установленных правил, процедур и технологических операций [Рис. 8].
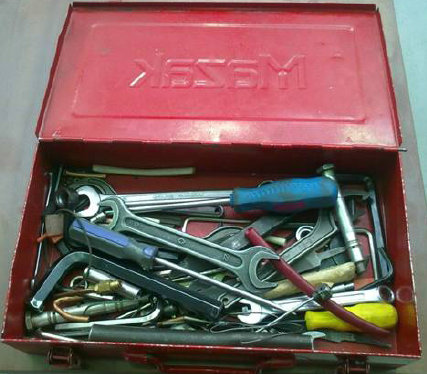
Рис. 4 - До
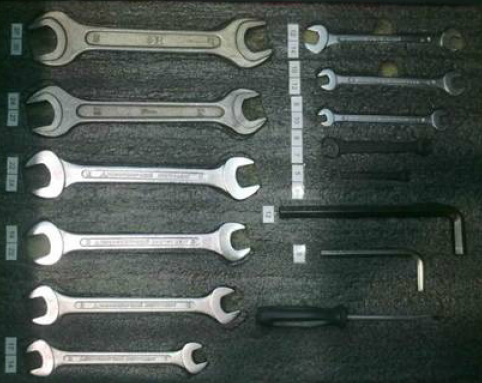
Рис. 4 - После
Пример «Сортировки»: "До" и "После"
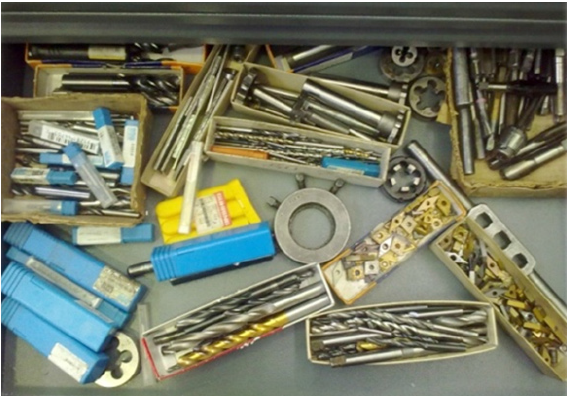
Рис. 5 - До
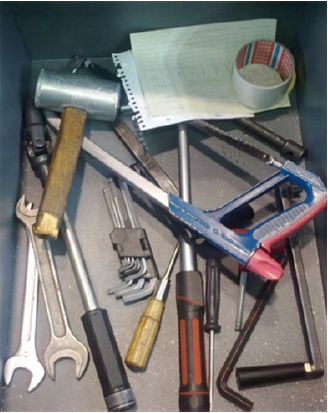
Рис. 5 - До
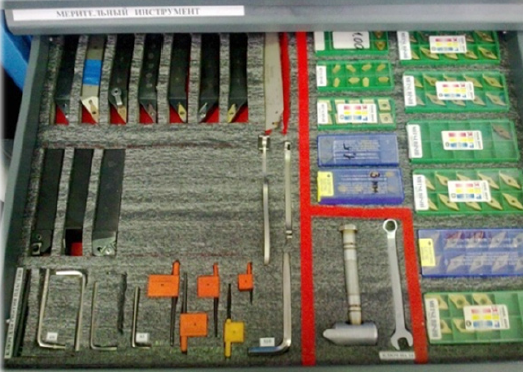
Рис. 5 - После
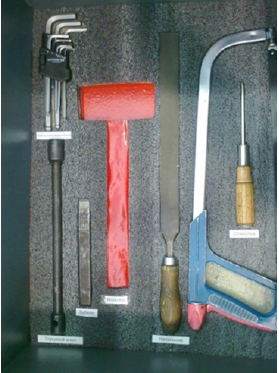
Рис. 5 - После
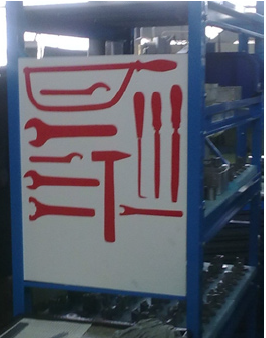
Рис. 5 - После
Пример «Соблюдения порядка»: Организация хранения "До" и "После"
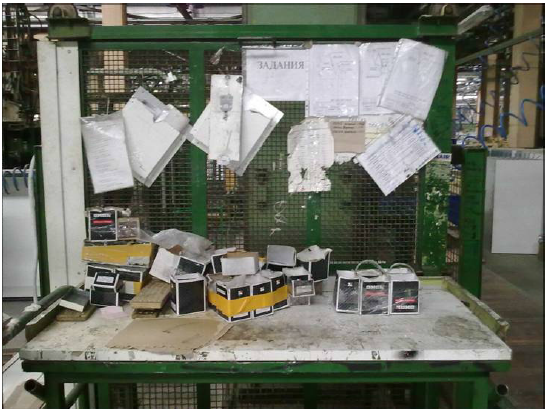
Рис. 6 - До
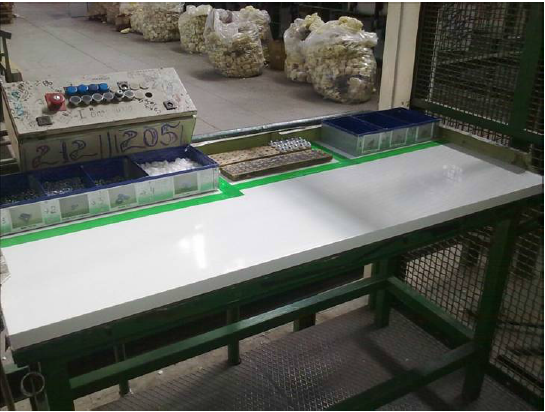
Рис. 6 - После
Пример «Содержание в чистоте»: "До" и "После"
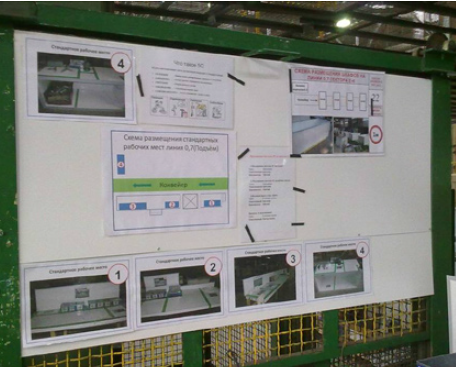
Рис. 7
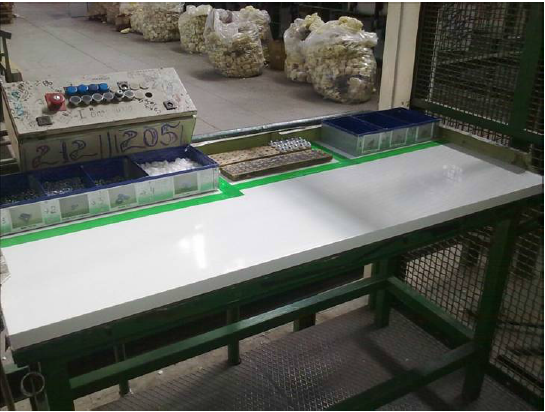
Рис. 7
Пример «Стандартизация»: Визуальные стенды участков
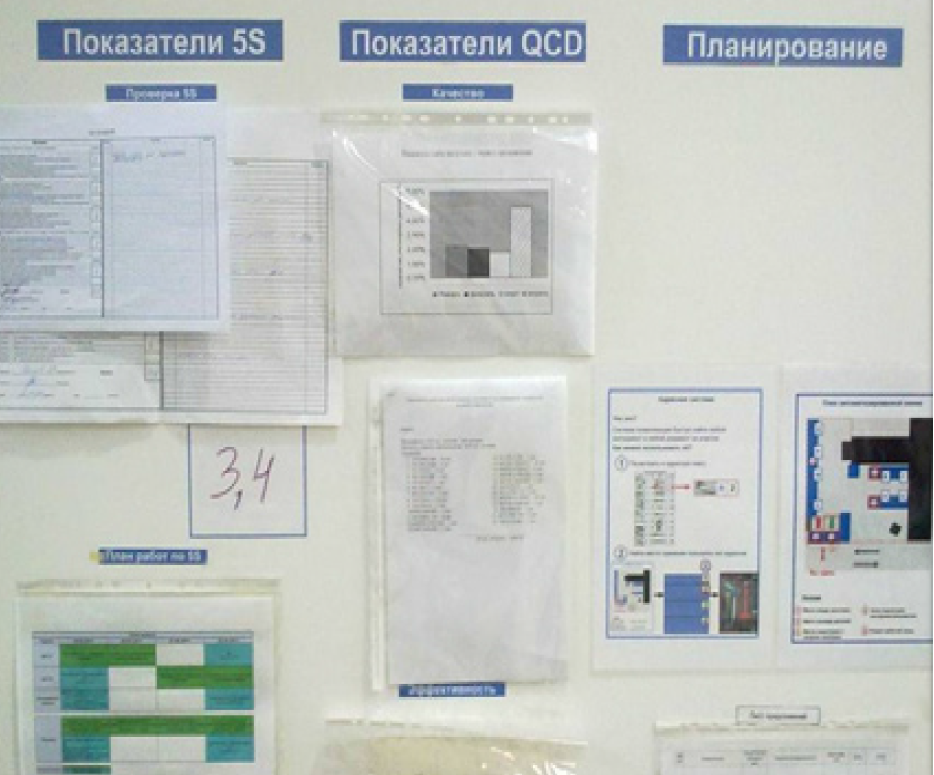
Рис. 8
Пример «Совершенствования»: Стенд показателей работы линии
Философия 5S – это не просто «стандартизация порядка», — это философия малозатратного, успешного, бережливого производства. Это система порядка! Ее цель:
Сделать рабочее место максимально «прозрачным», видимым, и понятным для «соседей» и для самих рабочих.
Быстро определять, что не так на рабочем месте, диагностировать проблемы.
Правильно организовать рабочее место для эффективной работы.
Повысить безопасность работы.
И самое важное, это базис для последующих улучшений!
Этап 2: Второй производственный цикл – применение концепции 5S
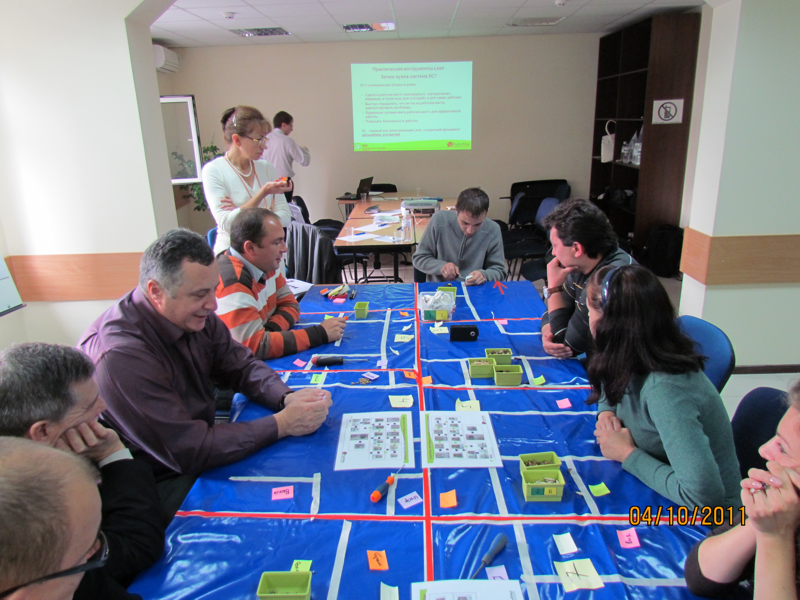
Фото 11
Изучив теорию применения первого инструмента Lean – 5S, приступаем к практическому его применению.
Теперь мы наводим порядок: сортируем и раскладываем детали по отдельным емкостям; организуем рабочее пространство всех производственных участков. Все участки разделены между собой; на каждом организовано рабочее место: есть зона для деталей, поступающих с предыдущего участка; есть детали для сборки, причем все детали рассортированы; есть зона инструментов; зона готовых для передачи на следующий участок полуфабрикатов, визуальная инструкция для сборки [Фото 11]. Нужно отметить, что каждый участник должен был организовать рабочее место, исходя не только из собственного удобства, а ориентируясь на то, что на этом месте может работать другой исполнитель. Лучший способ проверить качество организации рабочего места – поменять всех работников между собой и пересадить их на новые и еще не знакомые рабочие места.
Мы стартуем 2-й цикл – применение в производстве системы Lean 5S
В нашем производстве стало больше порядка, хотя все также все лихорадочно спешат сделать как можно больше. В этот раз первая партия вилок готова через 12 мин, а за 15 мин мы выпустили 10 вилок. У нас уже не было брака, и наши показатели эффективности несколько улучшились. Во-первых, возросла доля времени на создание добавочной ценности в суммарном затраченном на производстве времени, и как следствие снизилась стоимость одной вилки [Таблица 2].
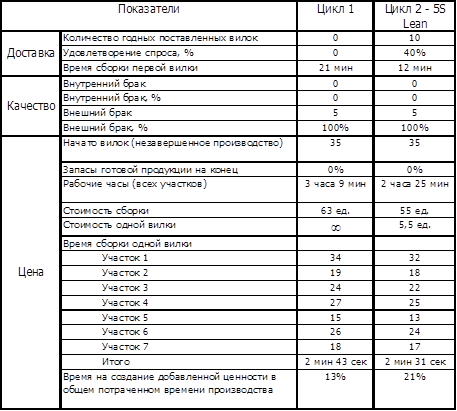
Вывод 2: Теперь 21% из общего рабочего времени было затрачено на создание добавочной ценности. Вот это да! Только применив методику Lean 5S (наведя порядок на рабочих местах), мы в два раза повысили эффективность производства. Конечно, в реальных условиях это соотношение может быть несколько другим (оно может быть и меньше и больше), однако и этот полученный результат впечатляет. Однако, радоваться все равно рано: заказчик хотел получить 25 вилок за 15 минут, а мы произвели только 10 вилок. Улучшив производство, мы все равно не смогли добиться главного, а именно удовлетворить спрос клиента. Завод уже второй месяц остается без зарплаты.
Двигаемся дальше.
Теория: Второй практический инструмент Lean – устранение потерь
Знакомимся со вторым практическим инструментом Lean – концентрация на потребностях клиента и устранение потерь. Как мы уже отметили ранее, потери — это любое действие, которое потребляет ресурсы, но не создает ценности для потребителя.
Lean выделяет 7 видов потерь:
Потери из-за перепроизводства.Производство лишних материалов и изделий, превышающее потребности покупателя
Потери времени из-за ожидания.Задержки, простои, любое время, в течение которого продукту или работнику необходимо ждать (помощи, инструментов, комплектующих, обработки…)
Потери при ненужной транспортировке.Лишняя транспортировка (между участками, складами...)
Потери из-за лишних этапов обработки.Лишние этапы, процедуры и виды работ, не создающие потребительской ценности
Потери из-за лишних запасов.Хранение лишнего сырья, незавершенных изделий и готовой продукции
Потери из-за ненужных движений, перемещений.Действия людей и оборудования, не добавляющие ценности продукту (на рабочем месте или в офисе)
Потери из-за выпуска дефектной продукции.Производство дефектных изделий, подлежащих уничтожению или переработке
Этап 3: Третий производственный цикл – избавление от потерь
Мы снова садимся за круглый стол и начинаем размышлять, что же нам мешает добиться нужного уровня выпуска? Мы меняем изначальные правила:
отменяем ограничение размера партий, теперь делать и передавать можно по одной штуке;
отменяем ограничение на помощь участка участку. Так как узкими местами нашего производства являются три рабочих места - это участок 1 (32 сек), участок 4 (25сек.) и участок 6 (24 сек). Тех, кто находится рядом с этими участками, попросили в свободное время оказывать этим участкам помощь;
отменяем правило перемещения деталей, двигаясь по часовой стрелке вокруг стола. Теперь детали с участка на участок можно просто передавать через стол.
После смены правил переходим к практике, стартуем 3-й цикл – применение в производстве методик Lean борьбы с потерями. На это раз мы произвели 25 вилок за 12 минут, т.е. полностью удовлетворили спрос, и еще остался резерв времени. Показатели эффективности производства улучшились существенно. Время на создание добавочной ценности в суммарном затраченном на производстве времени возросло до 50% (более, чем в двое по сравнению с предыдущим циклом), и как следствие себестоимость одной вилки снизилась тоже более, чем в двое. [Таблица 3].
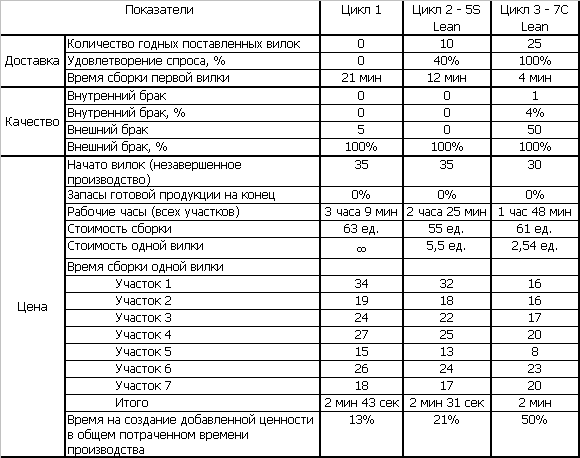
На практике, чем более неуклонно мы будем бороться с потерями, тем с каждым циклом мы будем получать все лучшие результаты. В идеале, мы должны полностью избавиться от потерь [Рис. 9].
Вывод 3: То, что мы получили снижение себестоимость одной вилки более, чем в два раза при одновременном увеличение доли времени на создание добавочной ценности в суммарном затраченном на производстве времени тоже более, чем в два раза наталкивает на интересные мысли. То, что зависимость существует, мы уже не сомневаемся. Является ли эта зависимость прямой? Надо будет проверить это на практике. Сэкономленное время после большого цикла улучшений

Проанализировав результаты, мы поняли, что основной причиной задержки производства был размер партии в 5 штук. В последнем цикле мы создали практически идеальный вариант единичного потока изделия, что и сыграло свою роль. Но, даже достигнув таких выдающихся результатов, мы не можем останавливаться, т.к. не можем точно спрогнозировать время сборки. Кто может сказать, сможем ли мы собрать такое же количество вилок за то же время в следующий раз?
Поэтому, самым эффективным решением является вытягивающая система.
Теория: Вытягивающая система. Канбан
Lean предполагает защиту клиентов от проблем производства и одновременно защиту производства от изменений требований клиентов. Поэтому, основные правила:
Управляйте производством с помощью вытягивающей системы, чтобы приспособиться к требованиям клиентов.
Балансируйте мощности, чтобы сократить время производства, выполнить работу в срок и сделать процесс более эффективным.
Вытягивающее производство (pull production) — это схема организации производства, при которой объёмы продукции и сроки ее изготовления на каждом производственном этапе определяются исключительно потребностями последующих этапов (в конечном итоге — потребностями заказчика).
Вытягивающую систему впервые в производстве применил Тайити Оно на заводе Toyota, «подсмотрев» ее в американской супермаркете. Всем знакома ситуация – на полках выставляется товар, подходит покупатель, берет одну или две единицы товара. Постепенно полка опустошается. Для рабочего, который должен следить за наполнением полок, этот момент является сигналом о том, что надо подвезти товар. Естественно, если никто с полки товар не берет, то ставить его туда не будут. Эту очевидную закономерность - спрос диктует предложение, - Тайити Оно и воплотил на заводах Toyota.
Основные понятия, которые используется для построения вытягивающей системы – "Время Такта" и "Канбан". "Время Такта" – это интервал времени или периодичность, с которой потребитель запрашивает готовую продукцию от поставщика (производителя). Этот показатель служит для синхронизации рабочего ритма производителя в соответствии с потребностью заказчика и рассчитывается по формуле:
Время такта = Доступное рабочее время / Покупательский спрос
Канбан (по-японски означает "рекламный щит", "вывеска") - это сигнальный механизм вытягивающей системы. Этот механизм сигнализирует операторам, что и когда они должны сделать. В качестве канбана могут также использоваться контейнеры, ярлыки. Примеры визуальной системы Канбан представлена на [Рис. 10].
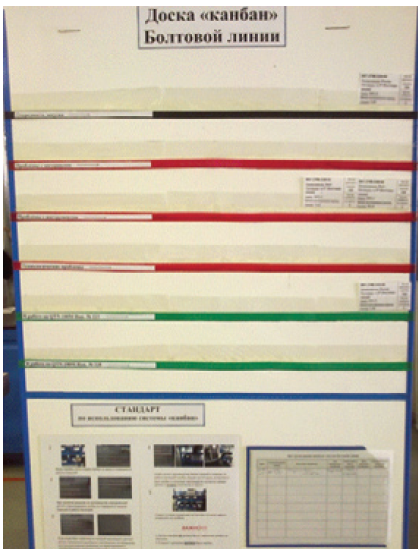
Рис. 10
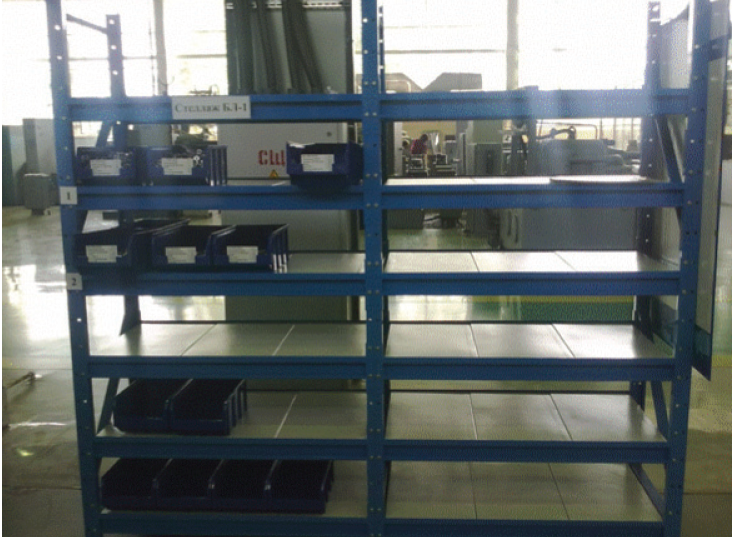
Рис. 10
Пример визуальной системы Канбан
Этап 4: Четвертый производственный цикл – система вытягивания
И снова практика. Сейчас мы подготавливаем наше «производство» для работы в системе вытягивания. Теперь у нас всего 5 участков (мы сократили количество участков). Они синхронизированы по мощности. А выпускать мы будем 15 белых и 10 черных вилок. На каждом участке есть визуальная инструкция, разложен инструмент, производственный задел и элементы для сборки на участке. Всего на всех участках в производственном заделе (незавершенном производстве) находится 4 вилки (2 в готовой продукции и 2 в НзП) (Сравните с 35 вилками, которые у нас были на предыдущих циклах). Все разложено и визуализировано таким образом, чтобы участки поставщики видели, когда на следующем за ними производственном участке возникает потребность в сборочных единицах, которые делают они.
Время такта на нашем сложнейшем предприятии равно 36 секунд.
Cтартуем
Основное правило: пока не пришел клиент и не взял продукцию со склада, производство ничего не производит. Клиент забирает продукцию со склада (или черную, или белую вилку). На последний участок сборки сразу же передается сигнал о необходимости пополнения склада готовой продукции. Последний участок начинает собирать недостающую готовую продукцию для пополнения запасов. Для этого он берет в работу незавершенную сборочную единицу, поступившую с предыдущего участка, и начинает сборку. Предыдущий участок получает сигнал о необходимости восстановления запаса последнего участка сборки, и тоже начинает свою работу, используя для этого свой задел. Участок, который стоит перед предыдущим видит, что тот начал работу и видит, с чем тот работает, и начинает свою работу и т.д.
В первые минуты этого цикла мы все еще волновались и старались сделать все очень быстро. Но буквально сразу же заметили, что спешить вовсе не нужно. Все участки успевают выполнять свою работу, рабочий ритм достаточно комфортный, спешки нет, участники успевают еще и пообщаться между собой, прокомментировать происходящее. А главное: спрос клиента вовремя удовлетворен, работа выполняется эффективнее (сокращено количество участков и работающего персонала), как следствие, произошло сокращение затрат. В этот момент наступает озарение. Оказывается можно работать по-другому. Раньше теоретически знали, читали о возможностях Lean методов управления. Но так, чтобы, вот так испробовать на себе, - просто дух захватывает, мы в восторге.
Теория: Что такое Lean организация
Мы подводим итоги дня и формулируем определение «Что такое Lean организация»
Lean организация – это система 5S, визуальное управление и стандартизация работы; это борьба с потерями и решение проблем; и вытягивающая система управления производством (Рис. 11). Чем выше мы поднимаемся по пирамиде, чем упорнее внедряем Lean, и тем более высокого качества достигаем, тем больше сокращаем сроки производства и снижаем себестоимость.
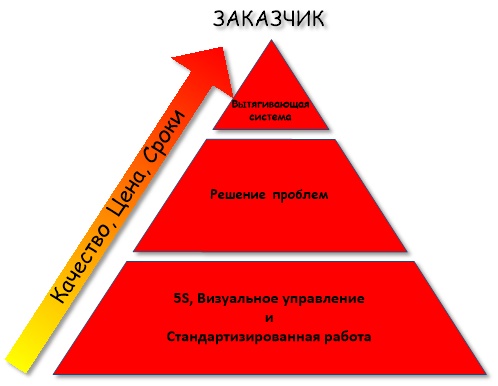
Мы также формулируем основные Принципы Lean:
Удовлетворение клиентского спроса;
Постоянное сокращение потерь;
Постоянный поиск новых способов совершенствования;
Работа в заданном ритме, балансировка мощностей и использование вытягивающей системы;
Поддержка и развитие инициативы;
Распространение знаний и достижений;
Интеграция, комбинирование и формализация всех процессов.
И в завершении мы выводим квинтэсенцию концепции Lean:
Lean не означает работать БЫСТРЕЕ
Lean не означает работать БОЛЬШЕ
Lean означает работать ИНТЕЛЛЕКТУАЛЬНЕЕ